Аннотация
The Vietnamese food industry produces a lot of coffee pulp, which is a valuable and abundant source of agricultural by-products. It contains a lot of cellulose, which can be converted into bioethanol. However, coffee pulp needs an extensive pretreatment to reduce the amount of lignin and hemicellulose while retaining the initial cellulose composition. This study compared several pre-hydrolysis and pre-fermentation pretreatment methods which involved H2SO4, NaOH, microwaves, and white rot fungus Phanerochaete chrysosporium.The hemicellulose dropped by 43.8% after the acidic pretreatment, by 47.1% after the alkaline pretreatment, and by 12.8% after the microbial pretreatment. The lignin contents dropped by 4.2, 76.6, and 50.2% after acidic, alkaline, and microbial pretreatment, respectively. The removal of hemicellulose and lignin in the coffee pulp was much more efficient when two or three of the pretreatment methods were combined. The microwave-assisted acid and alkaline pretreatment was the most efficient method: it removed 71.3% of hemicellulose and 79.2% of lignin. The combined method also had the highest amount of reducing sugars and glucose in hydrolysate. Additionally, concentrations of such yeast inhibitors as 5-hydroxymethyl-2-furaldehyde (HMF) and furfural were 2.11 and 3.37 g/L, respectively.
The acid pretreatment was effective only in removing hemicellulose while the alkaline pretreatment was effective in lignin removal; the fungal pretreatment had low results for both hemicellulose and lignin removals. Therefore, the combined pretreatment method was found optimal for coffee pulp.
Ключевые слова
Coffee pulp, hydrolysis, lignin, hemicellulose, reducing sugars, acidic pretreatment, alkaline pretreatmentВВЕДЕНИЕ
No ethanol can be obtained from lignocellulose biomass without some kind of pre-fermentation pretreatment which converts carbohydrate polymers in lignocellulose into simpler sugar. This conversion usually involves hydrolytic enzymes. Lignocellulose biomass possesses heterogeneous and very complex properties, e.g., cellulose crystallization, degree of coincidence, humidity, surface area, bonding level of lignin and hemicellulose, etc. As a result, this biomass requires special processing to be able to regulate the hydrolytic activity of the enzyme. The pretreatment also decreases the amount of lignin and hemicellulose in the raw material while retaining cellulose components and reducing the crystallization of cellulose (Fig. 1).
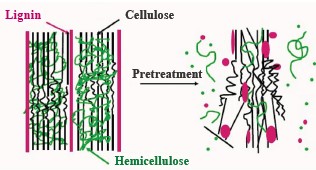
Coffee pulp is one of the most abundant sources of lignocellulose biomass in Vietnam. Coffee pulp is the first by-product obtained from wet processing during coffee production. The global coffee production is responsible for around 22 million tons of fresh pulp per year, 2.4 million tons of mucilage, and about 8.6 million tons of parchment. The Vietnamese coffee industry dumps about 0.5 million tons of dried pulp into the environment [2]. A combined effort of technology, economics, and environmentalism is needed to cope with this waste issue. The main chemical components of coffee pulp include cellulose (25.88%), hemicellulose (3.6%), lignin (20.07%), protein (9.52%), total sugars (9.18%), and ash (6.29%). Coffee pulp has a high nutritional value, which makes it a valuable source of animal feed. However, coffee pulp also contains some non-nutritional ingredients, such as tannins (8.69%) and caffeine (0.78%), which are bad for food metabolism [3].
Several recent studies reported that coffee pulp has a great potential for ethanol production [4–6]. Unfortunately, it also contains a lot of hemicellulose and lignin, which bind to cellulose (Fig. 2) to form a barrier that protects cellulose molecules from the attack of chemicals and enzymes. Therefore, ethanol production needs new pretreatment methods to remove lignin while retaining cellulose in the raw material prior to hydrolysis and fermentation.
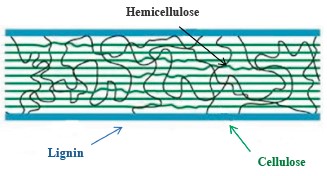
The list of pretreatment methods that remove lignin and hemicellulose includes acid pretreatment, alkaline pretreatment, steam explosion pretreatment, microwave pretreatment, hydrothermal pretreatment, and microbial pretreatment [7–12]. Chemical and thermal pretreatment methods all share the same disadvantages, such as environmental pollution, equipment corrosion, high cost, and production of yeast inhibitors. Microbial pretreatment method overcomes these disadvantages but has a long processing time and low effectiveness of lignin and hemicellulose removal.
Lignin is one of the main components that make up plant and algal cells. It is the most abundant component found in tree trunks, and it is often called “wood matter”. In coffee pulp, lignin accounts for about 17.5–20.07%, while lignin contents in straw, corn cores, sugarcane, and grass are 4.65, 15, 20, and 12–18%, respectively [3, 13]. Coffee pulp has a higher lignin content than other sources of lignocellulose biomass, which is a major challenge for its pretreatment processing before hydrolysis and fermentation. Therefore, ethanol production needs more in-depth surveys of pretreatment methods and their combinations that would remove lignin and hemicellulose components while retaining cellulose.
ОБЪЕКТЫ И МЕТОДЫ ИССЛЕДОВАНИЯ
Biomass samples. Fresh coffee berries were collected in Pong Drang commune, Krong Buk district, Dak Lak province, Vietnam, in November and December. They went through a rubbing machine to remove the peel. After that, the pulp was left to dry at 60°C for 12 h until the humidity was 5–8% prior to being ground in a disc mill. The resulting powder was sifted through a multi-layer sifting system with sieve diameters of 0.25, 0.5, 1, and 2 mm. The powder that did not sift through the two-millimeter sieve grid underwent re-crushing. The study involved only the powder that went through the sieve grids of 1–2 mm (Fig. 3).
Chemicals, enzymes, and microorganism strains. The research involved the following chemicals:
– DNS Reagents (Guangzhou, Guangdong, China);
– CTAB (sigma-Aldrich, Singapore);
– EDTA (Guangzhou, Guangdong, China);
– lignin (Sigma-Aldrich, USA);
– CMC (Sigma-Aldrich, USA);
– TBP (Sigma-Aldrich, USA);
– glucose (Sigma-Aldrich, USA);
– Viscozyme® Cassava C (Bagsvaerd, Denmark): > 450 EGU/g;
– glucosidase (Novozyme 188) (Novozyme, Denmark): > 750 CBU/g; and
– Phanerochaete chrysosporium (Southern Institute of Biotechnology and Microbiological Application, SIAMB, Ho Chi Minh, Vietnam).
The raw material was pretreated in a sterilized steamer at 140°C for 45 min and cooled to room temperature before being filtered to collect the solid residue [14, 15]. The residue was washed several times with water until neutral pH and dried at 60°C for 12 h. Then, we placed dried material into a 500-mL round bottom flask and added 2% (w/w) NaOH solution (2 g NaOH per 100 g of raw material). The alkaline pretreatment lasted 20 min at 120°C and was followed by the microwave pretreatment at 300 W for 20 min [8, 10, 16, 17]. The pretreated material was then filtered, washed in neutral pH water, and dried. The control was only pretreated with hot water under the same conditions. The effectiveness of the pretreatment process was tested using surface SEM scans for the remaining fiber content and the reducing sugar in the pretreatment solution.
The concentrations of cellulose, hemicellulose, and lignin remaining in the pretreated material were calculated according to the equation below [7]:
Fungi pretreatment method. Whiter ot fungus P. chrysosporium was cultured in a semi-solid medium, which contained 2 g of rice bran, 8 g of coconut, 25 g of fishmeal, 25 g of oil cake, and 0.15 g of sugar rust (Fig. 4). The cultivation lasted 7 days. After that, the mass was filtered and centrifuged at 5000 rpm to obtain the fungal biomass. The pretreatment with P. chrysosporium took place at 35°C with the biomass to raw material ratio of 1.5%. A portion of the raw material was taken for cellulose, hemicellulose, and lignin quantification after 10, 20, 30, 40, and 50 days.
Hydrolysis method. We put 15 g of the pretreated raw material into a 250 mL Erlenmeyer flask and added 150 mL of citrate buffer (0.05 mol/L, pH 4.8), 25 FPU/g of Viscozyme Cassava, and 34 CBU/g of Novozyme 188. The hydrolysis occurred on a shaker at 150 rpm under 50°C and lasted 72 h. The hydrolysis mix was centriged at 2500 rpm for 10 min to collect the supernafutant for the reducing sugar and glucose analysis [3]. The processing involved the control sample, in which raw material was omitted. The hydrolysis performance (YEH, %) was calculated according to the following formula [7]:
Analytical methods. The reducing sugar content was determined using the dinitrosalicylic acid (Miller/ DNS) method [19]. The glucose content was determined by optical measurement at a wavelength of 540 nm using an oxidase/peroxidase system [20]. The cellulose and hemicellulose content was determined using the ADF and NDF methods [21]. The lignin content was determined according to U.S. TAPPI standards (TAPPI T. 222 OM-02 Acid-insoluble lignin in wood and pulp). The filter paper (FPU, U/mL) assay tested the saccharifying of cellulase: it was based on the hydrolysis of filter paper by cellulase solution [22]. The amount of glucose produced was determined using the dinitrosalicylic acid method [19].
The carboxymethyl cellulase (CMC, U/mL) assay for endo-β-1,4 glucanase measured the carboxymethyl cellulase hydrolysis by cellulase solution [22]. The amount of glucose produced was determined using the dinitrosalicylic acid method [19].
The cellobiase assay (CBU, U/mL) involved cellobiose hydrolysis by cellulase solution [22]. The amount of glucose produced was determined using the dinitrosalicylic acid method [19].
Statistical analysis. The experiments were randomly arranged and performed in triplicates with one or two variables. We employed the ANOVA software to conclude the discrepancy between the average of the tests. The Statgraphics Centurion 15.2 software was used to process the obtained statistics. The average and standard deviation was calculated using the Excel software. The results of the previous experiment were selected as fixed parameters for the experiments to follow.
РЕЗУЛЬТАТЫ И ИХ ОБСУЖДЕНИЕ
Formation of reducing sugar in pretreatment solution. Pretreatment methods increase the area of biomass surface, improve the porosity of raw materials, reduce cellulose crystallization, and remove hemicellulose and lignin. Both hemicellulose and lignin are important factors in the formation of lignocellulose biomass, and they bond with cellulose. A single pretreatment method is only good for a certain aspect but provides no resolution of the aforementioned requirements.
Therefore, a combination of many pretreatment methods can perform several tasks at once: save cellulose, reduce its crystallization, increase the surface area of contact with hydrolyzed enzymes, remove more lignin, and recover more hemicellulose.
The combination of acid and alkaline pretreatments in different orders yielded unexpected results. Most samples pretreated with alkaline, acid, or fungus res Pr ted in a much larger content of reducing sugar in the pretreatment solution compared to the water-pretreated control samples. In particular, the acid pretreatment produced a higher amount of reducing sugar when pretreated with alkaline (Fig. 5).
Previous studies of lignocellulose biomass pretreatment showed that the lignocellulose biomass pretreated with Phanerochaete chrysosporium gave a low removal efficiency of 20–40%. Meanwhile, acid or alkaline pretreatment proved to be more efficient because the processing time was shorter. However, the processing temperature was much higher, which required complex and expensive equipment. Moreover, the acid or alkaline pretreatment methods resulted in a greater cellulose loss than the microbial pretreatment and could produce some yeast inhibitors. Therefore, an optimal pretreatment method or th30 combination depend on the nature of the raw material and the objective, and a proper combination of different pretreatment methods can provide a greater efficiency compared to a single method.
Changes in cellulose, hemicellulose, and lignin content. The reducing sugar content in the pretreatment fluid is not the only factor to be considered when comparing different pretreatment methods. A more comprehensive comparison involves the changes in fiber composition, especially the decline of lignin and hemicellulose. Other important factors include the formation of yeast inhibitors and the content of reducing sugars that appear during hydrolysis.
Figure 6 shows that the coffee pulp pretreated with H2SO4 2% (w/w) demonstrated a decrease in hemicellulose content, which dropped from 3.67 to 2.06% (equivalent to 43.8% reduction of hemicellulose). It also triggered a minor change in lignin content: only 4.18% was decomposed. The coffee pulp pretreated with 2% H2SO4 (w/w) was further pretreated with 2% NaOH (w/w). And as a result, the hemicellulose content went on decreasing and dropped to 1.15%, which was equivalent to a 68.6% reduction after two pretreatment steps. The lignin content saw a dramatic decrease with 77.5% of lignin being decomposed, which was equivalent to a 78.5% reduction after two pretreatment steps.
In reverse order, the hemicellulose content from coffee pulp pretreated with 2% NaOH decreased from 3.67 to 1.94%, which was equivalent to a 47.1% reduction, and the lignin decomposed by 76.6%. The coffee pulp was further pretreated with H2SO4, which resulted in a 54.7% reduction of hemicellulose and a 77.3% reduction of lignin after two pretreatment steps (Fig. 6).
Thus, different orders of chemical use yielded different results in coffee pulp pretreatment. Figures 5 and 6 show that the use of acid and alkaline order in pretreatment was more effective than the opposite order. The reducing sugar content in the pretreatment liquid and the reduction degree of the hemicellulose content in acid-alkaline pretreatment were both higher than those in the alkaline-acid pretreatment. Probably, the hemicellulose hydrolysis under the action of diluted acid was the same as cellulose hydrolysis. Hemicellulose was initially hydrolyzed into long oligomers, short oligomers, or monomers, depending on the temperature, acid concentration, and hydrolysis time [7].
In our experiment, hemicellulose was hydrolyzed mostly into oligomers under the action of diluted alkaline, and the number of monomers was very small. Therefore, the reducing sugar content and the reduction level of hemicellulose content in the acid-alkaline pretreatment was higher than those in the alkaline-acid pretreatment.
The pretreatment of lignocellulose biomass with diluted alkaline increased the contact surface area and reduced both coincidence and crystallization by separating the bonds between lignin and cellulose or between hemicellulose and cellulose or by disrupting the structure of lignin (Fig. 7c).
Figure 7 also illustrates the difference between the raw sample and the processed sample. The raw sample had a hard structure which was very compact and nonporous. The sample processed by diluted alkaline showed increased porosity and a larger surface area, which was due to the removal of lignin and hemicellulose.
Furfural and 5-hydroxymethyl-2-furaldehyde (HMF) formation in hydrolysis solution. The pretreatment with diluted acid or diluted alkaline at high temperatures (> 140°C) resulted in a partial hydrolyzation of cellulose and a complete hydrolyzation of hemicellulose into single sugars, e.g., glucose, xylose, arabinose, mannose, galactose, as well as acetic acid. It could also cause a partial breakdown of lignin into phenol derivatives, i.e., para-hydroxyphenyl, guaiacyl, and syrignyl. In addition to that, this pretreatment method formed 5-hydroxymethyl-2-furaldehyde (HMF) and 2-furaldehyde (furfural). Organic acids, such as acetic acid or triflulororacetic acid (TFA), appeared as a result of the decomposition of pentose and hexose [7].
Of all these intermediate products, furfural and HMF are toxic to ethanol fermentation yeast. Therefore, they had to be removed or minimized. These toxic substances often develop immediately after the pretreatment process and partially dissolve in the pretreatment solution while the rest remains in the raw material residue. Therefore, they need to be removed immediately after the pretreatment or eliminated in the hydrolysis solution prior to fermentation. Removing them immediately after the pretreatment could be difficult because they are almost evenly distributed and penetrate deep inside the raw material, which means a complex extraction. Removing them during hydrolysis seems more effective because hydrolysis is a process of extracting and diffusing toxic substances from the raw material. Therefore, removing furfural and HMF in the hydrolysis solution is more cost-effective than in the raw material.
Furfural appeared as a result of decomposing pentose sugar, which was mainly xylose. HMF resulted from the breakdown of hexose, mainly glucose and fructose. Figure 8 illustrates the furfural and HMF content in the hydrolyzed solution. The pretreatment with 2% H2SO4 at 140°C for 45 min provided the highest content of furfural (3.61 g/L) because diluted acid had a hydrolysis effect on hemicellulose to form xylose, which continued to decompose into furfural under high temperature. Meanwhile, two samples pretreated by acid-alkaline and acid alkaline-microwave pretreatment methods had a slightly lower furfural content because both treatments involved a neutral soaking process. As a result, water washed away and damaged a lot of furfural. The pretreatment with 2% NaOH at 120°C for 20 min also produced the highest HMF content of 2.43 g/L because alkaline had a partial hydrolysis effect on cellulose to form glucose, which was then broken down into HMF at high temperature.
The furfural and HMF contents in hydrolysis solution correlated with the cellulose and hemicellulose contents, which degraded after the pretreatment. The microbial pretreatment samples showed no signs of furfural or HMF in the hydrolysis solution because the temperature was as low as 35°C, and no acid or alkaline was involved. As the hydrolysis process by cellulase also presupposed low temperatures, no furfural or HMF were detected. The control sample was only pretreated in hot water at 140°C without acid, alkaline, or microwaves. In this case, only a small amount of hemicellulose and cellulose were hydrolyzed and decomposed into furfural and HMF (Fig. 8).
In most pretreatment methods, when the furfural and HMF content exceed 1 g/L, they have a strong inhibitory effect on microbial cell growth, especially yeast [23]. To limit their formation, pretreatment usually involves low temperatures, which affects the pretreatment efficiency. Therefore, if the pretreatment process is thermal, furfural and HMF should be removed from the hydrolysis solution prior to fermentation.
Formation of reducing sugars and glucose in hydrolysis solution. A comprehensive effectiveness test of coffee pulp pretreatment cannot be reduced to the targeted lignin or hemicellulose removal and the percentage of cellulose retained. It should involve such factors as the reduction of crystallized cellulose, the structural hollowing, the surface contact area, etc. These factors improve the hydrolysis process and control the formation of some yeast inhibitors. All of the aforementioned considerations are to be verified through the material hydrolysis process after the pretreatment process is carried out.
Therefore, we compared the effectiveness of the pretreatment processes using the content of glucose and reducing sugars released under the action of commercial cellulase enzymes, represented here by Viscozyme Cassava C and Novozyme 188 (Novo, Denmark). The hydrolysis process occurred under the following conditions. The hydrolyzed temperature was 50°C at pH 4.8. The shaking mode was 150 rpm, and the hydrolyzation time was 72 h. The concentration of Viscozyme Cassava was 25 FPU/g cellulose and that of Novozyme 188 was 34 CBU/g β-glucosidase, based on dry shell weight [24].
The hydrolyzed liquid was centrifuged at 2500 rpm for 10 min. Figure 9 shows the results of the analysis of glucose and sugar content.
The purpose of the pretreatment process was to increase the sensitivity of cellulose to the hydrolyzed enzyme system. Therefore, the glucose and reducing sugar were the two components that characterized the action of the cellulase system on the cellulose component found in the coffee pulp after hydrolysis. According to Fig. 9, all the experimental samples demonstrated a better hydrolysis performance than the control sample, which involved water pretreatment under the same conditions. The glucose and reducing sugar reached the highest contents when the combined pretreatment followed the order of acid → alkaline → microwave. The glucose content was 31.39 g/L, and the reducing sugar content was 43.26 g/L.
The microbial pretreatment demonstrated the lowest results when the glucose content dropped to 5.42 g/L, and the reducing sugar content was as low as 13.19 g/L. P. chrysosporium secreted some extracellular enzymes, mainly active lignin hydrolysis, into the environment during the pretreatment process with only 50.2% of lignin being hydrolyzed. This rate was much lower than in the case of the acid-alkaline-microwave combination when up to 79.2% lignin was removed. P. chrysosporium also failed to break down hemicellulose, but was able to alter the content and the crystal structure of cellulose molecules (Fig. 7d). Therefore, the material structure was less porous, and the contact surface area and the sensitivity to hydrolysis enzymes were low. This led to a less efficient hydrolysis performance in comparison with the acid-alkaline-microwave pretreatment.In addition, the hydrolysis performance of the enzyme was lower in the case of acid-alkaline pretreatment. The acid pretreatment resulted in 9.26 g/L of glucose and 19.58 g/L of reducing sugar. The alkaline pretreatment helped release much higher amounts of sugar than the acid pretreatment: the glucose content was 24.36 g/L, and the reducing sugar content was 37.33 g/L. The amount of reducing sugar in the alkaline pretreatment solution was lower than that in the acid pretreatment solution (Fig. 5). As the diluted acid pretreatment was the most efficient hemicellulose hydrolysis mode, the highest amount of reducing sugar appeared in the pretreatment solution. NaOH cut off the endomolecular ester bonds between hemicellulose and other molecules, including lignin. As a result, the material became porous, thus increasing the contact surface area and the amorphous region of cellulose [25].
Although the microwave pretreatment did not really degrade lignin and hemicellulose (Fig. 6), it somewhat changed the surface structure of material (Fig. 7e). Microwaves trigger two types of bipolar interactions and ion interactions which cause rotation/collision between the bipolar molecules and the ions present in the material. As a result, they generate heat and disrupt the supermolecule structure of lignocellulose biomass, both inside and outside [17, 26]. The results were truly surprising when the combination of acid-alkaline-microwave pretreatment methods followed by the hydrolysis yielded the glucose content of 31.39 g/L. The yield exceeded the result of the acid treatment by 64.9% and was by 22.8% higher than in the alkaline-pretreated samples. The reducing sugar content was 43.26 g/L, which was by 42.6% higher than after the acidic pretreatment and by 17.3% higher than after the alkaline pretreatment (Fig. 9).
Thus, the combined acid-alkaline-microwave pretreatment gave the best results based on the fiber composition, the content of reducing sugar, and the change in the surface structure. This method reduced hemicellulose by 71.4 to 1.05% (g/100 g db) and lignin by 79.2 to 4.17% (g/100 g db). The remaining material consisted of 77.49% cellulose (calculated according to the original cellulose content), ash, and some other substances (Fig. 10). After this pretreatment, the coffee pulp looked like yellow-brown soft foam and had good water permeability (≤ 85%) (Fig. 11)
ВЫВОДЫ
This study led to four important conclusions:
1. The combined acid-alkaline-microwave pretreatment method possessed the best lignin and hemicellulose removal efficiency.
2. The acid pretreatment method had the lowest loss of cellulose.
3. The combined acid-alkaline-microwave pretreatment had the highest concentrations of reducing sugars and glucose.
4. The pretreatment with white rot fungus Phanerochaete chrysosporium
was safe, inexpensive, and green, although the hydrolysis efficiency was not as high as after other pretreatment methods. In addition, it produced no yeast inhibitory substances during ethanol fermentation.
Вклад авторов
D.V. Phuong developed the research concept, designed the study, collected the data, and drafted the manuscript. L.T. Nguyen wrote the abstract and proofread the manuscript; both the authors performed the experimental work and designed the research methodology.
КОНФЛИКТ ИНТЕРЕСОВ
The authors declared no conflict of interests regarding the publication of this article.
БЛАГОДАРНОСТИ
The authors would like to thank the Institute of Biotechnology and Food Technology, Industrial University of Ho Chi Minh City, Vietnam, and their co-workers for the technical and equipment support of this study.
СПИСОК ЛИТЕРАТУРЫ
- Sheng Y, Lam SS, Wu Y, Ge S, Wu J, Cai L, et al. Enzymatic conversion of pretreated lignocellulosic biomass: A review on influence of structural changes of lignin. Bioresource Technology. 2021;324. https://doi.org/10.1016/j.biortech.2020.124631
- Coffee: World markets and trade. United States Department of Agriculture; 2020. 9 p.
- Phuong DV, Quoc LPT, Tan PV, Duy LND. Production of bioethanol from Robusta coffee pulp (Coffea robusta L.) in Vietnam. Foods and Raw Materials. 2019;7(1):10–17. https://doi.org/10.21603/2308-4057-2019-1-10-17
- Dadi D, Beyene A, Simoens K, Soares J, Demeke MM, Thevelein JM, et al. Valorization of coffee byproducts for bioethanol production using lignocellulosic yeast fermentation and pervaporation. International Journal of Environmental Science and Technology. 2018;15:821–832. https://doi.org/10.1007/s13762-017-1440-x
- Shankar K, Kulkarni NS, Jayalakshmi SK, Sreeramulu K. Saccharification of the pretreated husks of corn, peanut and coffee cherry by the lignocellulolytic enzymes secreted by Sphingobacterium sp. ksn for the production of bioethanol. Biomass and Bioenergy. 2019;127. https://doi.org/10.1016/j.biombioe.2019.105298
- Duarte A, Uribe JC, Sarache W, Calderón A. Economic, environmental, and social assessment of bioethanol production using multiple coffee crop residues. Energy. 2021;216. https://doi.org/10.1016/j.energy.2020.119170
- Solarte-Toro JC, Romero-García JM, Martínez-Patiño JC, Ruiz-Ramos E, Castro-Galiano E, Cardona-Alzate CA. Acid pretreatment of lignocellulosic biomass for energy vectors production: A review focused on operational conditions and techno-economic assessment for bioethanol production. Renewable and Sustainable Energy Reviews. 2019;107:587–601. https://doi.org/10.1016/j.rser.2019.02.024
- Woiciechowski AL, Dalmas Neto CJ, de Souza Vandenberghe LP, de Carvalho Neto DP, Sydney ACN, Letti LAJ, et al. Lignocellulosic biomass: Acid and alkaline pretreatments and their effects on biomass recalcitrance – Conventional processing and recent advances. Bioresource Technology. 2020;304. https://doi.org/10.1016/j.biortech.2020.122848
- Ziegler-Devin I, Chrusciel L, Brosse N. Steam explosion pretreatment of lignocellulosic biomass: A mini-review of theorical and experimental approaches. Frontiers in Chemistry. 2021;9. https://doi.org/10.3389/fchem.2021.705358
- Hoang AT, Nižetić S, Ong HC, Mofijur M, Ahmed SF, Ashok B, et al. Insight into the recent advances of microwave pretreatment technologies for the conversion of lignocellulosic biomass into sustainable biofuel. Chemosphere. 2021;281. https://doi.org/10.1016/j.chemosphere.2021.130878
- Scapini T, dos Santos MSN, Bonatto C, Wancura JHC, Mulinari J, Camargo AF, et al. Hydrothermal pretreatment of lignocellulosic biomass for hemicellulose recovery. Bioresource Technology. 2021;342. https://doi.org/10.1016/j.biortech.2021.126033
- Mishra S, Singh PK, Dash S, Pattnaik R. Microbial pretreatment of lignocellulosic biomass for enhanced biomethanation and waste management. 3 Biotech. 2018;8. https://doi.org/10.1007/s13205-018-1480-z
- Wang W, Lee D-J. Lignocellulosic biomass pretreatment by deep eutectic solvents on lignin extraction and saccharification enhancement: A review. Bioresource Technology. 2021;339. https://doi.org/10.1016/j.biortech.2021.125587
- Sahoo D, Ummalyma SB, Okram AK, Pandey A, Sankar M, Sukumaran RK. Effect of dilute acid pretreatment of wild rice grass (Zizania latifolia) from Loktak Lake for enzymatic hydrolysis. Bioresource Technology. 2018;253:252–255. https://doi.org/10.1016/j.biortech.2018.01.048
- Martínez-Patiño JC, Lu-Chau TA, Gullon B, Ruiz E, Romero I, Castro E, et al. Application of a combined fungal and diluted acid pretreatment on olive tree biomass. Industrial Crops and Products. 2018;121:10–17. https://doi.org/10.1016/j.indcrop.2018.04.078
- Łukajtis R, Rybarczyk P, Kucharska K, Konopacka-Łyskawa D, Słupek E, Wychodnik K, et al. Optimization of saccharification conditions of lignocellulosic biomass under alkaline pre-treatment and enzymatic hydrolysis. Energies. 2018;11(4). https://doi.org/10.3390/en11040886
- Hassan SS, Williams GA, Jaiswal AK. Emerging technologies for the pretreatment of lignocellulosic biomass. Bioresource Technology. 2018;262:310–318. https://doi.org/10.1016/j.biortech.2018.04.099
- Sun Z, Mao Y, Liu S, Zhang H, Xu Y, Geng R, et al. Effect of pretreatment with Phanerochaete chrysosporium on physicochemical properties and pyrolysis behaviors of corn stover. Bioresource Technology. 2022;361. https://doi.org/10.1016/j.biortech.2022.127687
- Miller GL. Use of dinitrosalicylic acid reagent for determination of reducing sugar. Analytical Chemistry. 1959;31(3):426-428. https://doi.org/10.1021/ac60147a030
- Sadasivam S, Manickam A. Biochemical Methods. New Delhi: New Age International (P) Ltd. Publishers; 1996. 272 p.
- van Soest PJ, Robertson JB, Lewis BA. Methods for dietary fiber, neutral detergent fiber, and nonstarch polysaccharides in relation to animal nutrition. Journal of Dairy Science. 1991;74(10):3583–3597. https://doi.org/10.3168/jds.S0022-0302(91)78551-2
- Ghose T. Measurement of cellulase activities. Pure and Applied Chemistry. 1987;59(2):257–268.
- Sun C, Liao Q, Xia A, Fu Q, Huang Y, Zhu X, et al. Degradation and transformation of furfural derivatives from hydrothermal pre-treated algae and lignocellulosic biomass during hydrogen fermentation. Renewable and Sustainable Energy Reviews. 2020;131. https://doi.org/10.1016/j.rser.2020.109983
- Agrawal R, Verma A, Singhania RR, Varjani S, Di Dong C, Patel AK. Current understanding of the inhibition factors and their mechanism of action for the lignocellulosic biomass hydrolysis. Bioresource Technology. 2021;332. https://doi.org/10.1016/j.biortech.2021.125042
- Periyasamy S, Isabel JB, Kavitha S, Karthik V, Mohamed BA, Gizaw DG, et al. Recent advances in consolidated bioprocessing for conversion of lignocellulosic biomass into bioethanol – A review. Chemical Engineering Journal. 2022;453. https://doi.org/10.1016/j.cej.2022.139783
- Chen Z, Wan C. Ultrafast fractionation of lignocellulosic biomass by microwave-assisted deep eutectic solvent pretreatment. Bioresource Technology. 2018;250:532–537. https://doi.org/10.1016/j.biortech.2017.11.066